On The German Auto Industry
A look at several things that are going on in the German auto industry—from new vehicles to stamping to building electric vehicles.
#electronics #economics
Turns out that German companies are really involved in an array of interesting activities, so it turns out that this entire issue is devoted to them.
This week On Automotive
- What’s an Iguana Have to Do With It? VW’s Tiguan
- Stamping for EVs
- Formidable Forging: the world’s largest mechanical forging line
- Audi: Rattle & Hum
- An Electric Mercedes. . .Minivan
- Chips, Converters & Bubbles
- Speaking of German Companies and EVs. . .job losses ahead
- Lasers and Batteries
- The Electric Trend
///
What’s an Iguana Have to Do With It?

The Tiguan, refreshed. (Image: VoA)
To say that crossovers are important to VW in the U.S. is to understate the case.
For Q1 21 crossovers accounted for 64% of all sales (the total sales were 90,853 and of that number, 58,259 were crossovers).
The number-one selling vehicle for VW in Q1 was the Tiguan, its compact crossover, which had sales of 27,265 units, a 23% increase over Q1 2020.
Interesting market fact: Hein Schafer, senior vice president, Product Marketing and Strategy, Volkswagen of America, says that they anticipate compact SUVs having a 28.1% share of market by 2030. The midsize SUV will be at 17% and the sub-compact 5.3%.
Strange nomenclature fact: Apparently the name Tiguan is derived from the German words for tiger and iguana. It is the result of a contest held by Auto Bild, a German car magazine.
The current-generation Tiguan was introduced in the U.S. in model year 2018.
The company has just announced a refresh of the vehicle, which includes changes to exterior and interior designs, as well as enhanced digital capabilities.
Changes include:
- New front fascia. The bumper and the grille are both modified. LED headlights are standard and there is an available LED light line that runs horizontally across the grille, visually connecting the headlamps. This is to become a new signature for VW models.
- Powered, sensor activated rear hatch. Standard LED taillights. The word “TIGUAN” is now on the hatch just below the VW badge, which is an approach taken on all VW models.
- New alloy wheels, ranging from 17 to 20 inches.
- Heated front seats are standard.
- R-Line models (of the four trims, the SE R-Line Black and the SEL R-Line are the top trims) feature smart phone-like “buttons” and sliders that provide haptic feedback
- Standard (except for the base model) IQ . DRIVE, the company’s suite of driver assistance technologies (Front Assist (forward collision warning and autonomous emergency braking with pedestrian monitoring), Active Side Assist (blind spot monitor), Rear Traffic Alert, Lane Assist, adaptive cruise control with stop-and-go, Travel Assist (semi-automated driving assistance), and Emergency Assist). The base model has standard Front Assist, Side Assist and Rear Traffic Alert.
Names elsewhere. One of the interesting things to know about the Tiguan is that it is a global product. In Germany, the Tiguan as they know it is not the same as the Tiguan in the U.S.: the U.S. model is what is considered to be the long wheelbase version. That’s called the “Tiguan Allspace” in Germany. It is referred to as the “Tiguan L” in China.
The difference between a German Tiguan and an American Tiguan? The latter is 8.6 inches longer. (The U.S. Tiguan, Tiguan Allspace and Tiguan L length: 185.1 inches.)
The Tiguans for the North and South American markets, as well as the Tiguan Allspace for Europe, are manufactured at the VW plant in Puebla, Mexico. The Tiguan L for the China market is built in Shanghai.
Schafer’s description of the Tiguan: “Sporty and elegant.”
///
Stamping for EVs
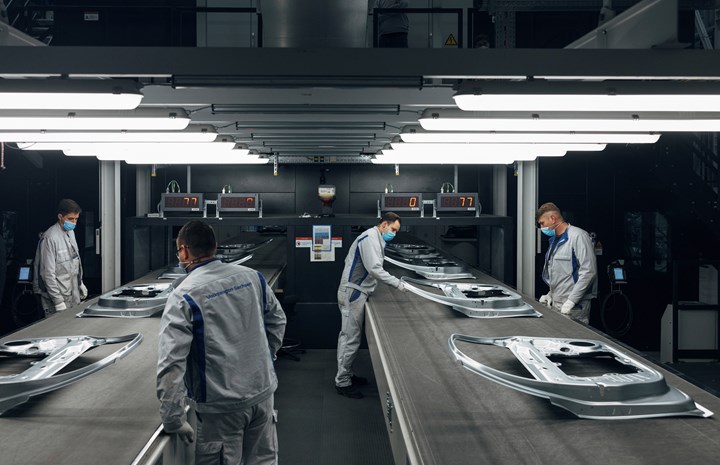
Body panels for VW EVs being stamped in Zwickau press shop. (Image: VW)
While on the subject of Volkswagen, last week it inaugurated an expansion of the stamping facility at its Zwickau assembly plant.
A €74 million expansion.
Zwickau underwent a €1.2 billion transformation that will be completed this year to transform it into an all-electric-vehicle production facility.
The centerpiece of the expansion is a 6,900-tonne XL transfer press from Schuler, a five-station unit. It is 302 feet long, 72 feet wide and 39 feet high.
It will operate at 10,800 strokes per day. It will be used to produce the exterior body panels for the vehicles—like the ID.3 and ID.4—assembled at Zwickau.
The XL press will add capacity for about 10 million parts per year when it is in full operation in 2022. This means Zwickau has the capacity to stamp 30 million parts per year.
///
Formidable Forging
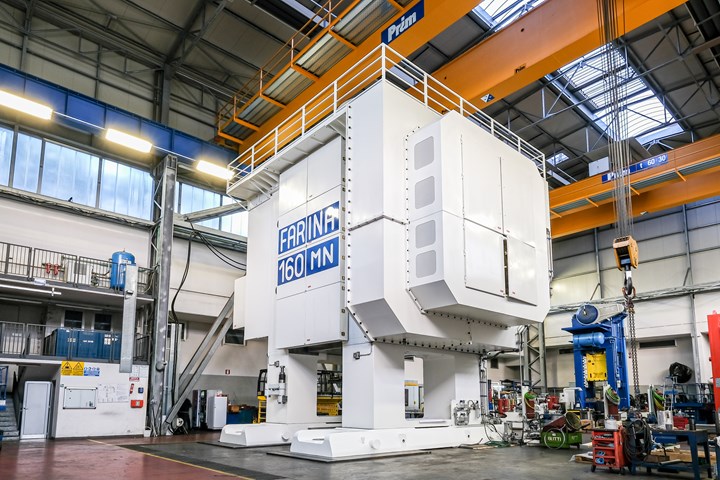
Forging press for auto parts. (Image; Schuler)
And speaking of giant pieces of pressworking equipment, thyssenkrupp Gerlach, an automotive supplier of things including forged crankshafts and con rods, will be receiving what Schuler claims is “the world’s largest mechanical forging line.”
The 16,000-ton press has a stroke of 600 mm.
The flywheel is located in the middle of the crown, which, according to Marco Gritti, the general manager of Farina, an affiliate of Schuler, “permits the press to be more precise in the forging process. The accuracy of the parts is therefore higher than with a traditional press.”
///
Audi: Rattle & Hum

Audi on hydropulse test stand. (Image: Audi)
Given that the word “noise” is the first in the NVH lineup (“noise, vibration, harshness”), for many people noise is evidently something that can be highly disturbing in a new vehicle.
To address unwanted noise, Audi has established in Ingolstadt what it calls the “Rustle and Rumble” team. This is a cross-functional group of people who otherwise work on functions ranging from chassis development to quality assurance.
They test Audi vehicles on the road, on a vibration track and on a servo-hydraulic test stand (photo above).
The hydropulse system permits the selection of frequencies that convey impulses from the wheels, through the chassis and into the vehicle.
Hear a squeak or rattle? Apparently it is likely to be from a vibration in the range up to 50 Hz.
And they’ve determined that a cause of a disruptive noise may start at the front door and getting transmitted to the rear such that it is only audible at the C-pillar.
Not straightforward.
Vocabulary of Noise. The Rustle and Rumble team has complied a list of the terms that may be helpful to other automotive sound engineers.
As well as to you, when you take your new vehicle in for service because of that noise:
Bedrock. Hum. Drone. Shimmer. Snag. Howl. Rattle. Jangle. Crack. Squeak. Creak. Crunch. Crackle. Whistle. Whoosh. Grind. Rustle. Clank. Knock. Buzz. Scrape. Whir. Vibration. Hum. Chirp. Hiss. Sizzle
///
An Electric Mercedes. . .Minivan

Tony Hawk, an electric board and a concept Mercedes EV. (Image: Mercedes)
In the U.S. market when it comes to vans from Mercedes, it is undoubtedly the Sprinter van—typically used for commercial service—that comes to mind.
In other markets, there are a variety of Mercedes products, including vans of a size that aren’t meant for 12 people or a load of plumbing equipment.
Mercedes is launching a compact van for “families and all those private customers, whatever their age, who enjoy leisure activities and need a lot of space and maximum variability without forgoing comfort and style,” according to Marcus Breitschwerdt, Head of Mercedes-Benz Vans.
Thrasher. Somewhat unusually, the company is using skateboarding legend Tony Hawk as part of its preparatory marketing efforts for the T-Class. Maybe that accounts for the “whatever their age.” And rather than showing the combustion-powered vehicle, the first variant they have revealed is a concept, the Mercedes Concept EQT.
“EQ” is the designation of the brand’s electric vehicles.
The Concept EQT has three rows and sliding doors on both sides.
Which sounds like a minivan.
And it is generally smaller than a Chrysler Pacifica.
Concept EQT: 194.7 inches long, 73.3 inches wide, 71.9 inches high.
Chrysler Pacifica: 204.3 inches long, 79.6 inches wide, 69.9 inches high.
Mercedes has announced no information about what will power the vehicle or what its range will be.
However, the Concept EQT does have an aluminum electric longboard housed in an aluminum compartment with a plexiglass lid flush with the load floor.
///
Chips, Converters & Bubbles

BMW i4—a new EV being released this year. (Image: BMW)
“The semiconductor supply situation will remain difficult, for instance. Additional headwinds are also expected due to rising raw material prices, particularly for rhodium and palladium and steel.”--Dr Nicolas Peter, Member of the Board of Management of BMW AG, Finance, Q1 conference call
Maybe EVs will help. Rhodium and palladium are used in catalytic converters, so maybe more electric BMWs will help there—although Peter also said during the call “Manufacturing costs rose compared to the previous year, mainly driven by the overall increase in sales volume and the growing share of electrified vehicles,” which seems to imply that there could be additional costs associated with electrified vehicles, about which he said they’ve sold “over 70,000” vehicles in Q1, which is 129.8% more than were sold in Q1 2020.
(Note: these are “electrified,” not necessarily fully electric. So a large percentage of them need catalytic converters: BMW expects to sell more than 100,000 fully electric vehicles this year. According to Oliver Zipse, Chairman of the Board of Management of BMW AG, they plan for “at least half” of global sales will be fully electric by 2030.)
Steel bubble? As for steel, last week U.S. benchmark hot-rolled coil steel prices hit about $1,500 a ton. Last year it bottomed out at $460 per ton. About the current price, Timna Tanners, a Bank of America analyst, told CNN Business: “This is going to be short-lived. It’s very appropriate to call this a bubble.”
Nicholas Peter probably isn’t the only one in the industry that hopes Tanners is correct.
///
Speaking of German Companies and EVs. . .
There is potential notable job losses coming in the German auto industry—at OEMs and especially supplier companies—by 2025.
So indicates the ifo Institute, which has completed a study for the German Association of the Automotive Industry (VDA).
Baby Boomer retirements will chosen some of the blow. It is expected that 75,000 German production workers—39,000 of which are at OEMs and the rest suppliers—will retire by 2025.
But if the anticipated change from internal combustion engines to electric motors occurs as anticipated, there will be a job loss of 178,000 employees.
Or, as Oliver Falck, director of the ifo Center for Industrial Organization and New Technologies, puts it, “The transformation that can be expected in headcount won’t be fully cushioned by the retirement of the baby boomers. Since companies are already aware of this gap, they have the opportunity to take appropriate measures in good time, such as retraining and further training.”
///
Lasers & Batteries

Using a blue laser to join battery components. (Image: Fraunhofer ILT)
Let’s face it: when it comes to making things like engines, the auto industry has a whole lot of experience.
When it comes to making things like lithium-ion batteries for vehicles (rather than, say, smartphones), the experience is a whole lot less extensive.
Research programs are being conducted by the Fraunhofer Institute for Laser Technology (ILT) to advance batter production.
HoLiB. In this battery production program, Fraunhofer ILT is determining the best laser process to connect battery anodes and cathodes to the contacts, or arrester tabs.
The anodes are copper. The cathodes aluminum. And the arrester tabs both.
So they’re using three lasers: A blue diode laser (450 nm wavelength). A green disk laser (515 nm). And an infrared fiber laser (1070 nm).
They are looking at a process where there is stacking of 20 anodes and cathodes, with the stacking being performed so that a single stack on a turntable is ready for laser welding within two seconds.
“The test of the three beam sources has already shown that the film stack can be welded through with process reliability,” says Johanna Helm, a Fraunhofer ILT research associate.
MikroPlus. This project is looking at the bonding of battery cells. The issue is one of the thermal sensitivity of the electrical contacts.
Too little welding energy and the connection doesn’t have the mechanical stability it needs.
Too much welding energy and the battery operation is imparted or service life shortened.
So they’re working with an infrared fiber laser pulsed in the nanosecond range to weld the copper, aluminum and steel materials.
German battery build-out. Last fall S&P Platts noted the construction of six major battery manufacturing facilities in Germany. SVOLT, CATL, VW and Northvolt, Opel and Saft, and Tesla are all building battery plants in Germany.
Presumably quick processing is a key factor.
///
The Electric Trend
During all of 2020 there were 124,097 electric vehicles—passenger cars and light utilities—produced in Germany, according to Inovev.
Obviously a pandemic year isn’t a good measurement, but there it is.
One way that might provide some clues about the dynamic in Germany is to compare the first quarter production for 2020 and 2021.
In Q1 2020 there were 14,691 EVs produced.
In Q1 2021 there were 35,512 EVs produced.
Clearly, there going to need to be a lot more batteries.
RELATED CONTENT
-
Ford GT Display Development
As you are unlikely to ever be in one of these: (and I’m not implying my odds for getting there are much better), you’re unlikely to ever see this, the 10-inch wide all-digital display in the Ford GT: Speaking to the development of TFT LCD display, Jamal Hameedi, chief engineer, Ford Performance, said, “Driver focus and attention are key with such high performance.
-
Autoline After Hours: The 2020 Cadillac XT6
Cadillac currently has three non-car vehicles in its lineup, the imposing and possibly venerable Escalade, the XT5, which started its existence as the SRX and is now crushing it in the market, and the most recent, the compact XT4, which is in a sweet spot for those looking to get into the premium portion of the market.
-
GM Develops a New Electrical Platform
GM engineers create a better electrical architecture that can handle the ever-increasing needs of vehicle systems