Using Simulation Software to Optimize Automotive Lightweighting
Automotive manufacturers are meeting CAFE fuel-efficiency standards through lightweighting, which requires simulation software for design engineers.

Automotive manufacturers can use an array of advanced techniques to remove material without reducing the structural integrity of the part. Simulation software enables designers to take full advantage of this advanced technology.
With increasing demands for fuel efficiency, lightweighting is coming into its own as a widespread, fundamental practice in automotive design. Its benefits speak loudly: simply reducing a vehicle’s weight by 10 percent improves its fuel efficiency by 3 percent, making fuel efficiency standards much easier to meet. However, it is only one of many design considerations that manufacturers must meet. Standards for safety and durability compete with lightweighting for the attention of the designer, but as techniques improve, the ability of auto manufacturers to meet these competing standards as efficiently as possible continues to increase.
Maximizing Fuel Efficiency with Lightweighting
Let’s look at the lightweighting technologies that automotive manufacturers can use to meet fuel-efficiency goals:

- Additive manufacturing – or 3D printing – is rapidly becoming extremely valuable to auto manufacturers because it enables the design and construction of complex parts with empty pockets. For example, 3D printers generate honeycomb pockets that reduce the weight of the structure, but also evenly distribute the stress on the part. This technique enables the user to create mechanically strong parts at significantly reduced weights in a wide variety of printable materials.
- Aluminum-to-steel welding, a recent development, opens new possibilities for mass management in automotive design. In addition to enabling designers to increase the amount of lightweight aluminum in a frame, it also eliminates the need for more fasteners, further reducing the overall weight of the vehicle.

- Composite materials like carbon fiber have primarily been used in high-end sports cars for decades, but the last ten years have seen a change. Stronger than steel and lighter by far, carbon fiber’s use in the automotive world had been hampered by costs, but recent developments have led to reductions in prices and improvements in production speed. Now, carbon-fiber parts are seeing much higher production volumes in the automotive world.
- Five-axis machining is a major boon to auto manufacturers, as it provides a lightweighting option for manufacturing parts that — unlike additive manufacturing — benefit from using forged materials. The five axes of movement enable the manufacturer to carefully carve out hollow areas to reduce the mass of the part.
- Microcellular injection molding is another technique that employs hollowing to lightweight parts. Through this method, an injection mold incorporates gas infusions into the molten plastic that expand on release into the mold, reducing weight between 20 and 40 percent. However, this technique is only available for plastic parts.
Lightweighting Simulation for Automotive Engineers
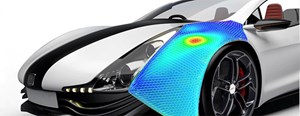
These technologies have drastically increased the degree of creative freedom many shops have in their approach to designing parts. However, lightweighting is not without complications. The tradeoff is that reducing the mass of a structure impacts every other mechanical aspect of design. A lighter material naturally has different structural tolerances, and manufacturers must consider these variances to meet the strict safety, durability and performance standards, all while keeping weight in mind. In an automotive landscape that sees these standards competing for the manufacturer’s attention, simulation of these complex parts is a must.
Because changing materials or hollowing a part impacts its strength and durability, it becomes necessary to test product designs through simulation software. Traditional simulation tools provide detailed feedback to assist in designing parts.

Topology optimization applied to a bracket identifies areas of the part that do not contribute to strength and stiffness so they can be removed from the design without affecting performance.
For example, Autodesk’s simulation software includes tools that evaluate stress and safety factors so that models can go through multiple iterations. This enables designers to confidently test the strengths of hollowed parts, lightweight materials and welded joints before ever making a physical prototype. The topology optimization feature is also a potent tool for lightweighting, as it can identify areas of a part that contribute the least to strength, flagging them for removal. This places lightweighting at the forefront of the designer’s mind early on in the process.
Access Hundreds of Design Options with Generative Design
GM embraced Autodesk’s generative design capabilities to significantly reduce the weight of parts for its vehicles without sacrificing strength.
Autodesk’s latest development for lightweighting is generative design. This feature provides inputs in which the user sets the parameters and constraints of part, then uses an algorithm to generate over 100 possible design solutions using nonstandard shapes and geometries. The designer can then select the design that best meets the needs of the part. Because the generative design feature combines full CAD, CAE and CAM suites, it enables the designer to use one program for the entire designing, prototyping and testing process.

Once the design process is completed, the manufacturer can determine which combination of the techniques above will best serve the final product. While the ethos of the past 30 years has been to design for manufacturing, these advanced technologies enable the manufacturer to adapt to the design. With efficiency standards increasing and the limits on what can be produced evaporating, advanced design platforms are necessary to meet the needs of the modern automotive manufacturer.
To view Autodesk’s complete guide to lightweighting, click here.
RELATED CONTENT
-
Choosing the Right Fasteners for Automotive
PennEngineering makes hundreds of different fasteners for the automotive industry with standard and custom products as well as automated assembly solutions. Discover how they’re used and how to select the right one. (Sponsored Content)
-
Increasing Use of Structural Adhesives in Automotive
Can you glue a car together? Frank Billotto of DuPont Transportation & Industrial discusses the major role structural adhesives can play in vehicle assembly.
-
on lots of electric trucks. . .Grand Highlander. . .atomically analyzing additive. . .geometric designs. . .Dodge Hornet. . .
EVs slowdown. . .Ram’s latest in electricity. . .the Grand Highlander is. . .additive at the atomic level. . .advanced—and retro—designs. . .the Dodge Hornet. . .Rimac in reverse. . .