9 Ways Additive Manufacturing Rises to the Advanced Mobility Challenge
Additive manufacturing (AM) is just one manufacturing method that drives advanced mobility forward and also has a history of embracing the digital connectivity demanded by this trend.
It might look like the automotive industry hasn’t changed much over the last two decades; and to many, the same can be said of the production of auto parts.
But this has begun to change. The industry is seeing major shifts in how we think about trends like autonomous vehicles, electric vehicles and more digitally connected transportation. Ridesharing is now widespread on a global level. Electric vehicles are becoming more commercially viable, and autonomous vehicles are seeing a swell in demand like never before. Drivers and riders alike are beginning to have a more digitally connected experience.

As a response, the need for advanced manufacturing and more sophisticated manufacturing techniques has grown in order to match this advanced mobility market. These advancements are already making an impact not only on how we experience automotive transportation, but how its parts are made.
One area that has seen tremendous influence is additive manufacturing (AM). EOS North America, leading the way in industrial 3D printing of metals and polymers, is dedicated to improving 3D printing efficiency. This includes working on higher productivity laser processes, achieving over 4X faster build rates for production, ultimately making mass-volume AM a reality in the automotive industry.
Automotive Design Challenges: Meet Additive Manufacturing Solutions
EOS is putting 3D printing limitations to the test. Here are nine unique challenges posed to the automotive industry and how additive manufacturing solved them with ease:
1. THE CHALLENGE: Reduce the number of steps and components for complex seat bracket.

GM used Autodesk's Generative Design to create hundreds of options for replacing a metal seat bracket (left). The end result (right) is a significantly lighter and more cost-efficient, 3D-printed part.
Partnering with Autodesk, General Motors sought to reduce the number of steps it took to produce a complex seat bracket by using additive manufacturing. Taking advantage of Autodesk Generative Design, GM created 150+ AM design options and selected one that took 8 metal welded and stamped components and reduced it to one 3D printed part. Through this design method and with the support of production on the EOS M 280, GM was able to significantly reduce part weight and increase part strength.
While the software certainly did most of the decision making, thus greatly reducing production time, additive manufacturing made it possible to take all eight separate components and transform it into a single part. This reflects time originally wasted on steps such as tool design, welding and assembly as well as quality control measures for each individual component.
2. THE CHALLENGE: Add more customization and personalization with car parts.

Additive manufacturing makes one-off custom products like this personalized name plate possible. (Source: MINI)

Custom door handles, like the ones shown here, are mirrored on each side, doubling the number of parts 3D-printed in a single build.
More and more luxury car buyers are looking for unique designs, flashy touches and finishes, parts that make the whole vehicle more personalized. But, with mass-produced automotive parts, this can be cost-prohibitive and wasteful. By 3D printing one-off parts such as personalized name inserts, aftermarket customization is as simple as digitally entering an order on demand and having a 3D part delivered quickly—in less than a week—without any excess inventory.
Another example is the limited edition door handle cover for DS Automobiles in a project paired with Spartacus3D. This exclusive design required only one hour of production time per part with 200 parts included in each build without any negative impact on quality.
3. THE CHALLENGE: Significantly reduce the weight of several engine parts.
In this example, a team of Renault Truck engineers and designers looked to additive manufacturing to reduce weight for their DTI 5 4-cylinder Euro 6 engine. Beyond just prototyping a sample model, additive manufacturing was used to virtually design and then successfully 3D print multiple metal parts—such as rocker arms and camshaft bearing caps—that were then successfully bench-tested for 600 hours within a Euro 6 engine. Ultimately, additive manufacturing contributed to a 25% weight reduction overall, and reduced the number of total parts by 200.
4. THE CHALLENGE: Produce quick turnaround parts with limited budget.
Race cars today are still one of the best additive manufacturing use cases because F1 cars typically have limited budget but are free from standardized automotive design restraints, and they’re more adaptive to innovative design changes.

This brake cooling duct provides cool air flow to the brake disc and calliper.
With the Renault F1 brake duct part, advanced additive materials were used to replace a carbon fiber component, providing significant cost and time reductions. Not only did the part need to be produced quickly, but the brake disc needed to withstand extreme temperatures, operating at around 400ºC. The final product, designed in CAD, was a strong, lightweight part made with nylon 11 and reinforced with carbon fiber that was melted into the plastic and powder fused together.
F1 racing isn't the only area that has seen increased use of additive. Motocross bikes, like those produced by Pankl Racing Systems, found major advantages to create strong, lightweight components that had never been possible before. Aside from lightweighting, AM made it possible to have a design printed, tested on the race course and installed for use within days.
5. THE CHALLENGE: Achieve thermal balance in high-pressure die cast tool.

Finished die cast tool with conformal cooling design.
Still today, die casting is the preferred method for producing aluminum powertrain and structural components in the automotive industry. However, one of the largest challenges is thermally balancing the tool during production. This is needed to limit the use of external spray, reduce cycle times and minimize casting defects and porosity.
With additive manufacturing on an EOS M 400-4, companies like EXCO Engineering can integrate cooling channels directly into the tool all in-house. In addition to outperforming conventional H13 by 3X, the tool went through 160,000 die-cast cycles before cracking to waterline. As a result EXCO saw tool life more than triple and has even developed unique ways of repurposing used components with AM.
6. THE CHALLENGE: Build production injection mold tool with cheaper materials.

If you buy a Chevy Silverado today and choose to include the new Bose speakers, chances are the covers of those speakers are an intricate mesh pattern. Traditionally, these parts were divided into two sections that would require a material called Porcerax, a porous metal, for the metal injection molding process. Not only expensive, this material presented a serious cycle time challenge.
With additive manufacturing and the help of newly developed materials, GM teamed up with Hi-Tech Mold and Engineering to reduce material costs while greatly reducing build time. Built in CAD and then built on an EOS M 290, the final part included conformal venting and cooling, and eliminated any need for special cleaning or maintenance.
7. THE CHALLENGE: 3D print strong, metal printed part in less time.

Collaborating with GKN Powder Metallurgy, EOS helped develop a new method for laser metal 3D printing with direct metal laser sintering (DMLS) to reduce production time and overall cost. The added bonus was to provide the design freedom necessary for more advanced applications.
This collaboration combined GKN’s high-productivity metal powder with the EOS Stainless Steel 316L VPro. Together they found an application with Senior Flexonics to produce high-volume, additively manufactured parts with high-function porosity for reducing part weight.
The High Productivity Process—also referred to as HighPro AM—includes an industrialized water atomized powder process, based on the EOS proven additive process. Beam and power stability were essential for consistent DMLS part quality and were further supported by the machine’s four-lasers.

The EOS M 300-4 provided the beam and power stability necessary for consistent part quality.
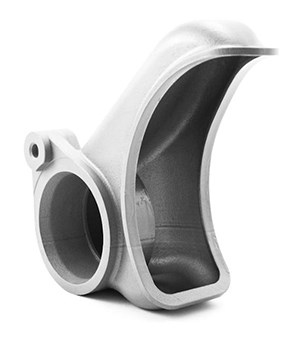
Built with the High Productivity Laser Process, this coolant inlet for automotive achieved the functional porosity it required with a significantly faster build rate.
While a shorter production time was itself a challenge, the product required all internal surfaces must hold pressure and prevent damage during welding and brazing.
The end product developed with this method was a coolant inlet for exhaust gas purification system used with both on-highway and off-highway trucking. For this particular part, conventional AM methods would require roughly 26 hours of production time, but with the HighPro AM process, that production time was reduced to only 6 hours. On top of trimming cycle time, prices were cut by 30%.

Pictured is the conventional additive manufacturing microstructure (left) compared to the more porous microstructure of the High Productivity Process (right).
8. THE CHALLENGE: Reduce human interaction with high-volume AM production.
The GKN Bonn, Germany plant is the poster-child for what a digitalized, human-interference free, high-volume AM production plant of the future could look like. The highly automated factory will be home to the additive production of spare and aftermarket automotive components, roughly planning for small series of around 10,000 parts made a year.
The goal is to create a flexible and modular procedure for AM production that optimized machine efficiency while reducing human interaction. The project titled, “Industrialization and Digitization of Additive Manufacturing (AM) for Automotive Series Processes” or IDAM for short, will be a milestone for metal 3D printing in the automotive industry.
9. THE CHALLENGE: Automate the entire 3D printing operation.
Together with Premium AEROTEC and Daimler, EOS helped to develop the next generation of AM with its Quad-Laser EOS M 400-4 machine. By introducing unprecedented levels of digitalization to the serial production process, from the delivery of metal powder to post-build processing, the NextGenAM project aimed to change the way additive can impact the future of automotive mobility.
As far as the role of EOS, many of these examples were customer driven. However, the stability job after job and repeatability of the EOS additive manufacturing platform is what made these customers turn to them. To learn more about EOS additive manufacturing solutions, click here.
About the Author
Jon Walker – Automotive Specialist and Business Development Manager
Jon Walker supports major automotive OEMs and suppliers as they integrate additive manufacturing into their supply chain. Throughout his career, he has worked with numerous Fortune 500 companies specializing in manufacturing to help them navigate their journey toward 3D printing adoption.
Prior to working at EOS, Jon managed sales activity in the Midwest at GF Machining Solutions, where he focused on increasing quality and reduce processing time for customer parts focusing on the mold and die industry.
To talk more about the future of AM in the advanced mobility space, contact Jon Walker at jon.walker@eos-na.com
RELATED CONTENT
-
Increasing Use of Structural Adhesives in Automotive
Can you glue a car together? Frank Billotto of DuPont Transportation & Industrial discusses the major role structural adhesives can play in vehicle assembly.
-
When Automated Production Turning is the Low-Cost Option
For the right parts, or families of parts, an automated CNC turning cell is simply the least expensive way to produce high-quality parts. Here’s why.
-
GM Seeks to Avert U.S. Plant Shutdowns Linked to Supplier Bankruptcy
General Motors Co. says it hopes to claim equipment and inventory from a bankrupt interior trim supplier to avoid being forced to idle all 19 of its U.S. assembly plants.