On Global EV Sales, Lean and the Supply Chain & Dealing With Snow
The distribution of EVs and potential implications, why lean still matters even with supply chain issues, where there are the most industrial robots, a potential coming shortage that isn’t a microprocessor, mapping tech and obscured signs, and a look at the future
#economics
EV Numbers and Potential Consequences
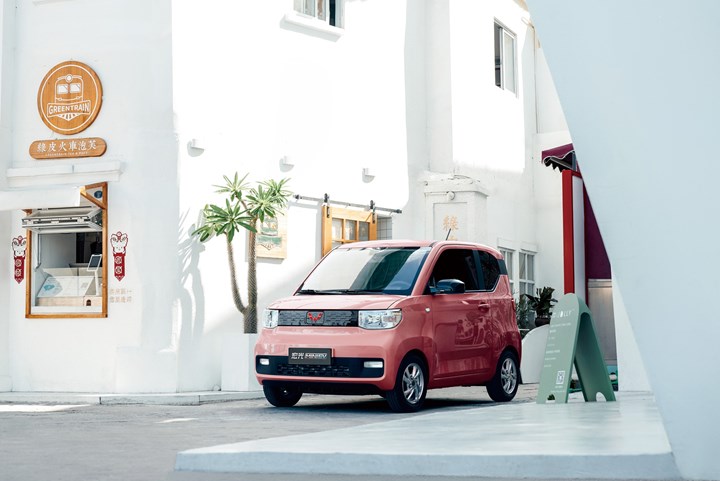
The Wuling Hong Guang MINI EV is by far the leading electric vehicle on offer in China—the combined sales of the Tesla Model 3 and Model Y don’t even reach it. Potentially something of interest for Europe, where people still drive small cars. (Image: Wuling)
The International Energy Agency reported that in 2020 Germans registered 395,000 electrified vehicles. 185,000 in France. And 176,000 in the U.K.
Or a total of 756,000.
Meanwhile, in the U.S., the number was 295,000.
To put this into context:
The populations of Germany, France and the UK are, respectively:
- 83 million
- 67 million
- 67 million
Or a total:
- 217 million
The population of the U.S.:
- 329 million
So as you can see, the density of electrified vehicles per capita is, well, a whole lot more dense in those European countries.
Announcements by GM and Ford indicate that they are going to work to catch up fast.
If one can speculate that Europe might be ahead of the curve that the U.S. will essentially follow, then speculative analysis from French firm Inovev regarding the transition to electrified vehicles is worth considering.
The firm created a forecast model to simulate what might occur in Europe by 2030.
It looked at factors including legislation for CO2 objectives and probable market demand.
Two scenarios emerged:
- To meet the regulations, OEMs would need to sell at least 40% full battery electric vehicles (BEVs) and 10% plug-in hybrid vehicles (PHEVs)
- 30% BEVs and 25% PHEVs would do it, too
The kicker:
Inovev’s reference scenario has it that the combined sales of BEVs and PHEVs in Europe might be 35% (25% BEVs and 10% PHEVs).
Which could be problematic to the OEMs because it wouldn’t reach the target.
But Inovev discovered something else that could prove to be difficult for the OEMs:
The firm points out that OEMs are showing a tendency of producing larger, more functionally complex vehicles. That’s because they tend to be more profitable.
This means small vehicles are not being offered as had been the case.
Two consequences. Neither particularly good:
This could lead to two consequences:
- Vehicle prices will rise to the point where there is diminished affordability. The overall new vehicle market will decline as people keep their vehicles longer or opt for alternative means of transportation.
- Because the European OEMs are not producing small cars, it may become “a royal road for the development of non-European carmakers in Europe, in particular Chinese carmakers, who do not necessarily meet the same objectives as European carmakers (search for profitability, in particular).”
So if it is assumed that the U.S. OEMs will increase EV production and, because of the additional cost of transitioning to the EV model from ICEs* they build primarily higher-priced vehicles (which we are seeing now with the chip shortage) and eliminate small cars (think only of what has happened to Ford’s car lineup), then they certainly better hope that tariffs are in place because that “royal road” could become a superhighway because cheap Chinese cars could come rolling in because that’s what the vast number of domestic purchasers can afford.
*Although everyone talks about battery costs declining and therefore reaching parity with gasoline power, let’s not forget about the sunk costs in tooling and equipment for gasoline-powered vehicles that must be accounted for by the OEMs and suppliers. A non-trivial cost.
///
Lean Still Matters
There are two pillars of the Toyota Production System:
- Jidoka. “Automation with a human touch.” A well-designed machine/system that can operate autonomously so that an individual can oversee several and can stop production should there be something wrong detected.
- Just-in-Time. An approach where materials/parts are where they need to be when they need to be there.
There are the Seven Wastes addressed by lean manufacturing:
- Overproduction
- Defects
- Motion
- Over-processing
- Waiting
- Transportation
- Inventory
So where are we?
Last fall global consulting firm AlixPartners estimated that due to supply chain disruptions—including semiconductors—the worldwide auto industry would lose the production of 7.7-million units and cost the industry $210 billion.
Mark Wakefield, global co-leader of the automotive and industrial practice at AlixPartners said upon the release of the forecast, “There’s no room for error for automakers and suppliers right now; they need to calculate every alternative and make sure they’re undertaking only the best options.”
I emphasized those last four words because they are important.
Arguably, some might think that their company had established its own version of the Toyota Production System and its countermeasures against the Seven Wastes, and are rethinking the just-in-time/minimal inventory elements.
After all, even Toyota lost production due to the chip shortage.
Disruptions aren’t new
Taiichi Ohno is the “father” of the Toyota Production system and he codified the seven wastes. Ohno lived and worked in Toyota City. Toyota City is close to Nagoya. Nagoya has not gone without natural disasters, like earthquakes.*
Obviously, earthquakes can cause supply chain disruptions, just like a pandemic can. Ohno probably wasn’t oblivious to that.
Yet he still promoted just-in-time and identified inventory as a waste.
One of the things that shows up year after year in the Plante Moran North American OEM-Supplier Working Relations Index is that Toyota, which is a perennial leader, has excellent relationships with suppliers.
When you work with someone on anything, odds are that things will go better than if you treat that person as a mere vendor.
When someone understands your approach to things—like having just-in-time and minimal inventory—and there is a level of respect, then that person is more likely to help you realize that, even when things go badly.
That mutual assistance is probably more valuable than warehouses full of whatever.
What inventory did
It is too easy for people to forget—or not even know—that it used to be in many OEM plants that massive amounts of inventory did nothing but serve to hide poor practices and bad quality.
So managers who think, “I’m not going to be caught without having [fill in the blank]; we’re going to purchase warehouses full of it—and because we’re going to be buying at such volume, we can push the supplier’s price down,” are likely to end up where they were before the conversion to lean practices.
To abandon lean now may seem like the right thing to do.
But it isn’t.
==
*Here’s something that is a real eye-opener, from the Disaster Mitigation Research Center at Nagoya University: “Nagoya City and the surrounding Chukyo area are vulnerable to natural hazard risks, particularly colossal earthquakes along the Nankai Trough plate boundary. The Japanese government estimates that there is a 70-80% chance of a massive earthquake occurring during the next 30 years. The area also has a history of damaging floods and storms.”
///
Industrial Robot Quiz
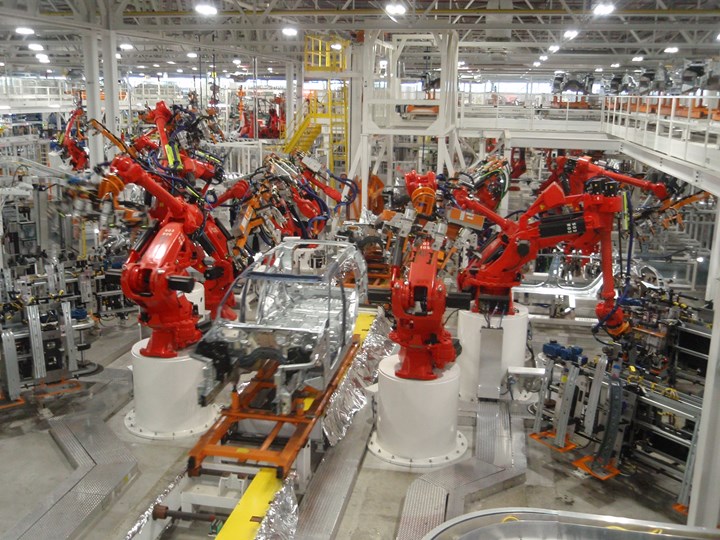
Inside the Stellantis Detroit Assembly Complex-Mack. (Photo: gsv)
It is hard to imagine an automotive body line without a phalanx of spot-welding robots on either side.
The auto industry has long been a leader in the implementation of industrial robots.
So a quick quiz.
What country has the greatest number of robots installed per 10,000 employees? (The list is alphabetized so don’t draw any assumptions from it.)
- Austria
- China
- Denmark
- Germany
- Japan
- Republic of Korea
- Singapore
- Sweden
- United States
. . . .(imagine something like the music played during “Final Jeopardy”. . . .
The answer, according to the International Federation of Robotics, which tabulates such things. . .
- Republic of Korea. It has a massive 932 robots per 10,000 employees.
The world average is 126 per 10,000.
The other four countries constituting the top five are:
- Singapore, 605
- Japan, 390
- Germany, 371
- Sweden, 289
The U.S. is in seventh place with 255.
Although Austria was put on the list simply so I could start with an “A,” know that with 205 it betters Spain (203), France (194) and several other countries.
Denmark actually ties China at 246.
Here’s something you might not have thought about regarding the implementation of robots:
According to Milton Guerry, IFR president, robots are actually beneficial to sustainability efforts for three reasons:
- They provide cost-efficient production of things like EV batteries and solar panels
- They contribute to throughput with fewer rejects, thereby lowering the carbon footprint associated with waste
- They reduce production system energy consumption thanks to energy-efficient arm and tooling design.
///
Semiconductors Today, Steel Tomorrow. . .
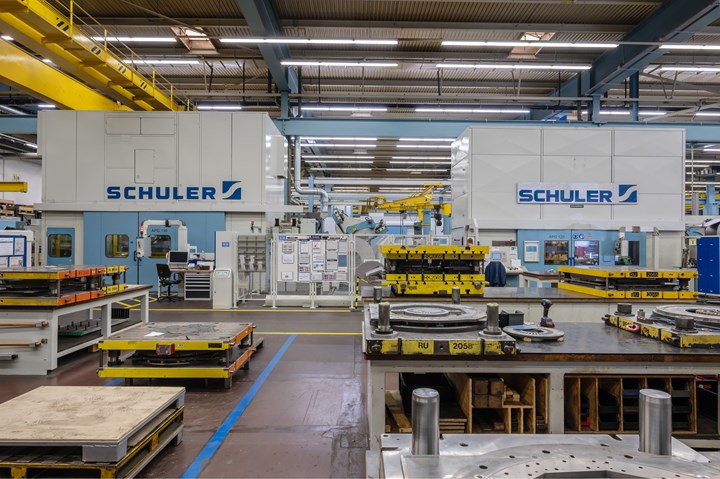
Siemens lamination stamping line in Nuremberg. The plant produces drives for mining and ships. (Image: Schuler)
It’s called “electric steel.” And yes, it has big implications for electric motors.
It could be a problem for companies who want to put those electric motors into their vehicles.
So researchers at IHS Markit have calculated what the future may hold.
What is it?
Electric steel is an iron-silicon alloy.
Of the 2-billion metric ton steel market, it represents about 1% of the total.
Two types
There are two types of electric steel:
- Grain-oriented electric steel (GOES). This material has unidirectional magnetization and is used for static machinery applications such as transformers.
- Non-oriented electric steel (NOES). This has multidirectional magnetization. It is used for rotating machinery, such as motors and generators. Not only is this used in the auto industry, but a variety of others, such as consumer appliances.
And a subset
There is an important subset of NOES that is used for electric vehicles traction motors, xEV.
The tricky part
In 2020 the global demand for xEV for hybrid and electric vehicle motors was 320,000 tons. It is anticipated by IHS to be 2.5 million tons by 2027 and more than 4 million tons by 2033.
Based on global mill capacity, it is expected that there will be a shortage of xEV between 2023 and 2026.
Getting more steel isn’t something that happens overnight. IHS says that it takes a steel company about three years to get a new facility operating.
So expansion needs to be greenlighted sooner rather than later.
The research firm thinks that there will be a 61,000-ton shortage in 2026 and, if there isn’t a capacity increase, shortages of 357,000 tons in 2027 and 927,000 tons in 2030.
Additional tricky factors
IHS Markit says that there are 14 steel companies on the planet that can make xEV.
And 88% of that capacity is in China, Japan and South Korea.
What’s more (or what’s less) is that there are only
- 20 motor core lamination stampers
- Five companies that can make the stamping presses for the automotive motor laminations
- Less than 10 independent tool shops that can produce the required dies
What to do
Countermeasures that IHS suggests for OEMs range from reconfiguring motor designs to minimize steel scrap to vertically integrating for motor production, including dealing directly with the steel suppliers.
///
Here’s Something You May Have Missed
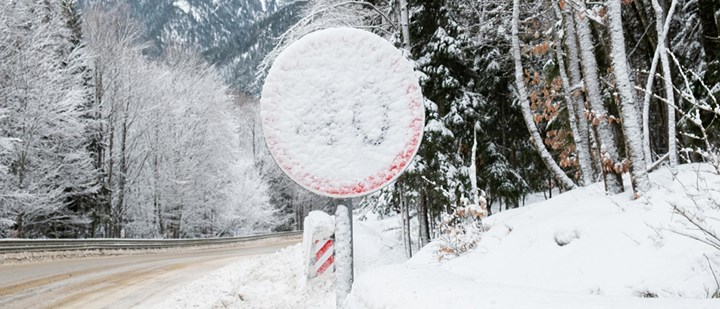
HERE ISA is meant to deal with things like this, which arguably a camera would have a tough time reading. (Image: HERE)
Some new vehicles have the ability to show on a screen (or two) the speed limit of the road you’re traveling on. Sometimes the information on the screen and the information on the sign are in conflict.
In July, new passenger and commercial vehicles sold in the European Union must be equipped with “Intelligent Speed Assistance” (ISA) capability, which, as described by HERE Technologies (which is owned, in large part, by VW Group, BMW and Daimler), helps “drivers to acknowledge and comply with legal speed limits on any given road.”
“Sorry, officer, but the display on my navigation system said 70 mph, not 55,” is an excuse that is going away. (OK, in the EU that would be 113 km/h and 89 km/h).
HERE has its ISA Map product on the market that will be deployed by most all EU OEMs. (Given its owners, odds are they get an employee discount.)
According to the company it can provide “speed limit information at any time, irrespective of environmental conditions.”
Apparently even when the sign is covered with snow.
///
A Winter Transport Alternative
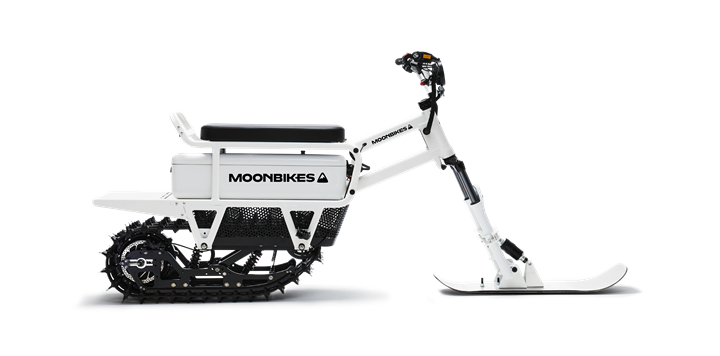
An EV for riding in the snow. (Image: MoonBike)
Speaking of snow. . .
A company based in Annecy, France, an alpine locale, is launching the MoonBike. An electric snow bike.
Origin story
Nicolas Muron, company founder, was visiting his grandparents in the French Alps. He realized that there are lots of ways to get around during the non-winter months. But wintertime comes with transportation limits.
While there are snowmobiles, Muron found them to be polluting, heavy and expensive.
So, the MoonBike.
An electric motor with a rated power of 3 kW. A weight of 87 kg (191 pounds). Base MSRP $8,500.
Dashing through the snow. . .
The MoonBike is 88 inches long, including the front skis. Top speed: 26 mph.
If operated in Eco mode it can travel 22 miles. If in Sport mode, 12 to 15 miles.
To keep the 2.5-kWh in battery reasonable operational condition (batteries don’t like to be frosty), it is housed in a heated container that protects it to temperatures as low as -13° F. It can be recharged with the standard setup in five hours, 45 minutes.
You’ve heard of this
While you probably haven’t heard of MoonBike, odds are you’ve heard of the company that is manufacturing the vehicles: Bosch.
///
Tech and Transport
And speaking of Bosch. . .
Technology progress is making the world a better place.
That’s what 72% of the people recently surveyed by Bosch—people in China, India, Germany, the UK and the US—think.
However, the Bosch Tech Compass found that this confidence in tech isn’t evenly distributed around the world.
- 83% of the people surveyed in China and 77% of those surveyed in India think tech is working to solve the major problems of our time
- 47% of those in the U.S., 37% in the UK and 29% in Germany think so
Here’s something Bosch found that should give those involved in automobility a sense of job security.
When asked how they’d like to get around in the future:
- 56% said a human-controlled car
- 40% airplanes
- 32% trains
Even though teleportation was an option (as in “Beam me up, Scotty”), the Germans were the biggest fans, with 39% saying that would be the preferred model The Indians were at the other end of the spectrum, at 10%.
So cars it is.
RELATED CONTENT
-
GM Is Down with Diesels
General Motors is one company that is clearly embracing the diesel engine.
-
Operator of Uber Self-Driving Car Wasn't Watching Before Fatal Crash
In-car video shows that the backup pilot of an Uber Technologies self-driving car was not watching the road just before the vehicle struck and killed a pedestrian last Sunday night.
-
On Electric Pickups, Flying Taxis, and Auto Industry Transformation
Ford goes for vertical integration, DENSO and Honeywell take to the skies, how suppliers feel about their customers, how vehicle customers feel about shopping, and insights from a software exec